Warnings & Limitations:For All Models
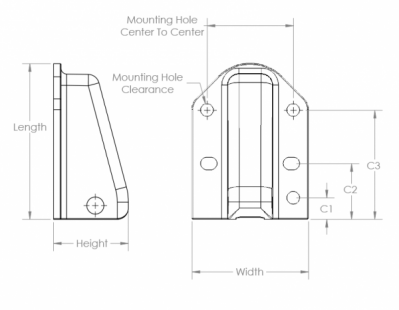
2. If the door is closed with insufficient force to trip the cam, the door will rebound.
3. If, for some reason, the cam is the "closed" (figure 5) position while the door is open, the door will rebound rather than latching when closed. This could be caused by a misaligned strike (all latches) and/or a loose handle (3H, 83H, 93H, 4H, 84H and 94H latches only), or by the cam being struck and rotated accidentally while in the "open" (figure 4) position.
4. If excessive force is used in closing (slamming) the door, the tendency of the door to rebound may be sufficient to cause the latch (and door) to reopen. A rebounding door would not normally cause a dangerous situation unless some aggravating condition is present. It is essential that the person closing the door is aware of the possibility of rebound, and is warned against violent slamming. The forces involved, and therefore the hazards, increase with the size and setting of the latch.
5. The door may open unexpectedly if material (such as a large casting) should fall and strike the interior of the door.
6. Brixon recommends that close attention be paid to the selection of hinges. If the hinges are not strong enough to withstand the maximum internal pressure, allowing for build-up due to time lag, the door may become a projectile.
7. The latches should be set at the lowest practical setting for your application. All enclosures differ from material integrity to the volatility of the explosion risk. Refer to the latest version of NFPA No. 68 to calculate the venting requirements of your specific vessel. Lower settings should always be used where practical for maximum safety.
8. Due to the inherent brittle nature of cast iron, high impact loads may fracture castings, possibly resulting in a flying fragment. This is not expected to occur under normal conditions, but is possible under unusually severe conditions.
WARNINGS AND LIMITATIONS:
SPECIAL PRECAUTIONS FOR 3H, 4H, 83H, 84H, 93H & 94H LATCHES
#91, #1(#1 model no longer sold) and #2 latches have pull type handles which do not affect the operation of the latch. The models 3H, 4H, 83H, 84H, 93H & 94H latches have handles which open the cam when used, but also allow the cam to open without the use of the handle. The following pertains to models 3H, 4H, 83H, 84H, 93H & 94H handle-type latches:When the handle is in the “closed” (down) position, the cam operates independently of the handle.
- When the handle is moved from the “closed” (down) position to the “open” (up) position, the cam is forced into the open position. The cam cannot be in the closed position with the handle up unless:
a) The handle is very loose
b) The internal socket set screw is broken or missing
c) The handle has been removed and reinstalled improperly.
d) The handle cross pin is broken or missing (83H, 84H, 93H & 94H)
If any of the above situations occur, a hazardous condition exists and must be corrected.
- If the handle is up while the door is being closed, the handle will snap back into the down position. In models 3H and 4H latches manufactured prior to 1979, especially chrome-plated latches, the handle may contact the door itself with considerable force, which would create a hazard to hands placed in the same area (See diagram below). Model 3H and 4H latch handles made after 1979, (similar to old handle except with larger rectangular stops), and model 83H, 84H, 93H & 94H latches stop well above the surface of the door if the handles have not been altered.
- Keep hands away from cams, rollers, handle stops, and away from areas between latch body and handle when closing. (See diagram below).
- If the socket set screw breaks, the handle becomes inoperable. Replacement of the socket set screw with one not identical to the original may cause a hazardous condition by destroying the independence of the cam and handle. Additionally, the bearing pin, handle, and cam must not be altered or used with any other latch. Each handle is individually fitted at the factory.
- Closing, and especially slamming, of the door with the handle up increases the possibility of shearing the internal socket set screw.
LIMITATIONS
- The #1 die-cast zinc model (no longer for sale) is not suitable for high temperature use; the all stainless steel #91 model is available for high temperatures.
- The #SP2A aluminum and #SP2B brass latches are recommended for spark proof applications.
- Standard 3H, 4H, 83H, 84H, 93H & 94H handles are not designed for multiple latch applications since all handles must be opened simultaneously to avoid undue strain on the latches, doors, and/or hinges. The #4HD and #410 heavy duty handles are recommended for such applications, or Brixon can custom fabricate linked latch assemblies.
- Brixon latches, like all other latches, will eventually wear out or need replacement due to inherent properties of the material used. The expected life depends strongly upon the conditions of use. If the latch is properly maintained, and in a non-corrosive and dry area, probable failure points are:a) Cracking of the casting near the bearing pin or base holes because of impact loads. This may result in a hazard in the case of a flying fragment. This is not common, but abuse of the latches makes it more likely.
b) The spring may lose temper because of prolonged heating or fatigue. This is not expected to be hazardous, but the door will open and/or rebound more easily than normal.If the latch is operated in an exterior or corrosive atmosphere, failure is more likely to be due to rusting of internal parts and/or castings. Corrosion of internal parts results in the probability of the latch mechanism “freezing” and is a major hazard in the event of an explosion. Corrosion of the casting will render it more prone to cracking or breaking under impact. (See MAINTENANCE) - Brixon Manufacturing Co. makes no claims for corrosion resistance beyond the properties of the materials used (see “NOTICE FOR LATCHES IN EXTERIOR OR INTERIOR CORROSIVE ENVIRONMENTS" section).
- Modifications of Brixon latches should not be made without consulting Brixon Manufacturing and without prior approval of Brixon Manufacturing Co.
- Field repairs of Brixon latches are not recommended.
- The following warnings pertain to Models 4HD and 410:a) Be sure return spring is operative to avoid crushing and denting danger at points “A” on closing.
b) Keep hands and other objects away from interior of resistance arm (points“B”).
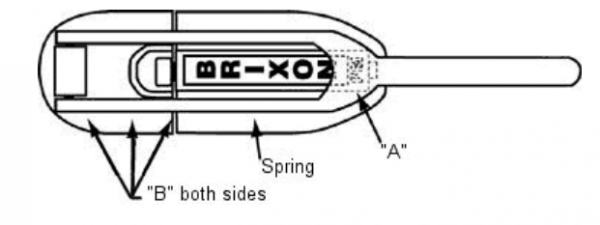
REPLACEMENT PARTS
The following replacement parts are available from the factory:- BODIES only (all models)
- STRIKES only (all models)
- HANDLES only - #2 only.
MAINTENANCE
Latches must have the explosion-venting feature tested periodically to insure that corrosion and/or build-up of foreign materials has not affected the mechanism. Under normal operation conditions, lubricate the bearing pin within the laminated cam with an SAE 30-50 high temperature oil EVERY TWO MONTHS. Lubricate the adjustment screw where it meets the laminated cam with SAE 30-50 high temperature oil ON INSTALLATION and repeat EVERY 12 MONTHS.NOTICE FOR LATCHES IN EXTERIOR OR INTERIOR CORROSIVE ENVIRONMENTS
Regular Brixon iron safety latches® (which are designed for interior use) are not recommended for exterior or corrosive applications. We recommend the Brixon® 90 Series all stainless steel investment cast latches for most corrosive applications.Maintenance of all Brixon latches is important at regular intervals.
1. Check to see that the latch is properly lubricated.
2. Open the door to make sure all parts are free to move.
The lubricating should be as follows:
- The crucial pivot joint, which is the bearing pin about which the laminated cam pivots, should be oiled with an SAE 30 to SAE 50 high temperature oil at least every two months.
- For use in cold areas we recommend using SAE 10-20 high temperature lubricant at least every two months.
- Lubricate the adjustment screw where it meets the laminated cam with an SAE 30 to SAE 50 high temperature oil on installation and repeat every 12 months.
- If you need further information on maintenance of Brixon® latches or if you wish to replace your latches with corrosion resistant latches, contact Brixon (information at bottom of previous page).
- Our model 91, 2, 3, 83, 93, 4, 84 & 94 latches are available with the following options for corrosion resistance.
Powder Coat | Chrome Plate | Electropolish | Polish/Buff Passivate | |
---|---|---|---|---|
Iron | X | X | ||
Aluminum | X | |||
Brass | X | X | ||
Steel | X | X | ||
Stainless Steel | X | X | X |
ADDITIONAL INFORMATION: CORROSION
Stainless steel** internal parts should last approximately five times as long as steel parts depending on the severity of the corrosive atmosphere. Trace metals in stainless steel tend to create chromium oxide coating which can be attacked by a wet chloride ion in marine conditions, and eventually rust will occur. Only the end-user can know the severity of corrosive conditions, and proper, regular maintenance becomes even more important under severe corrosive conditions.Aluminum will oxidize and discolor with time, but the discoloration will not affect the strength or overall life of aluminum. It may be difficult, however, to distinguish corrosion from discoloration.
Salt or corrosive atmospheres can cause aluminum to break down and become weakened. At the spot of corrosion, powdering will occur and also pitting of the latch body or strike. For this reason Brixon suggests that aluminum should be preserved with a protective coating if it is exposed to corrosive conditions. Black E Coat and Duplex anodizing are options available to preserve aluminum. (See "WARNINGS AND LIMITATIONS" section.)
Spark proof Brass latches are corrosion resistant and are available in our #2 model only. For marine conditions with heavy salt corrosion such as on ships or on oil rigs at sea, an aluminum bronze can be special ordered in the #2 model.
**Brixon uses the following stainless steel alloys: 15-7, 17-7, 18-8, 301 302, 303, and 304, 416 (hardened & passivated), and 316.
CUSTOMER SATISFACTION
We are continuing to innovate and explore ways in which the use of our products can provide measurable benefits to our customers and yours. Over the years, our reputation as problem solvers has helped us to form vital partnerships with some of the world’s most respected companies. Here is a partial list of companies who have relied on Brixon Manufacturing for explosion venting latches.Adolph Coors Company Amana Refrigeration ALCOA Alliant Tech Systems Archer Daniels Midland Company The Boeing Company Campbell Soup Company Corning Glass Works DOW Corporation Dupont Eastman Kodak Farmland Foods, Inc. Farr Company Firestone Flex-Kleen Corporation |
Ford Motor Company Garmat USA, Inc. General Electric George Koch Sons, LLC The Grieve Corporation Heinz Frozen Foods Hewlett-Packard Hormel Foods Corporation JBI Spray Booth & Systems, LP Kal Kan Foods Lever Brothers Company, Inc. Louisiana Pacific Corporation LGT Technologies Maaco Auto Painting & Body Works MacDonald Environmental Systems, Inc. |
M&M Mars, Inc. 3M Company Nestle Foods Corporation Oscar Mayer Foods Corporation Polaroid Corporation PPG Industries, Inc. Precision Quincy Corporation Reynolds Metals Company Rodrigue Métal Ltd Spraybooth Systems, Inc. Square D Company Trek Bicycle Corporation Uncle Ben’s, Inc. Weyerhauser |